Home on the Range Update
- Ian Thompson
- Jun 30, 2019
- 4 min read
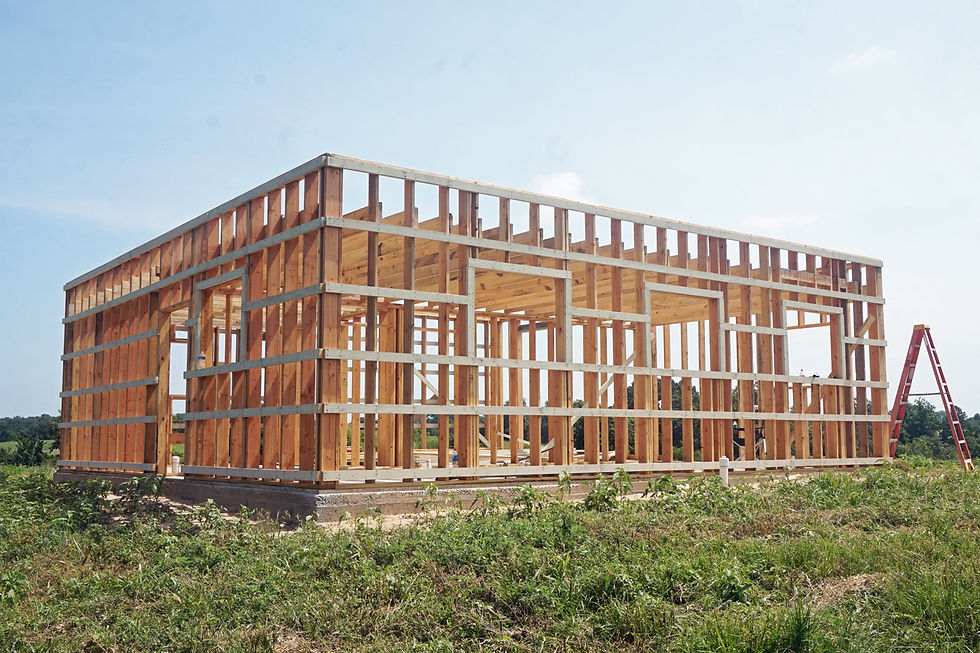
Back in February, we posted our plans to build our Green Home on the Range. The new home will be our only residence and will also provide an opportunity for guests to stay at the farmstead without having to roll out a sleeping bag on the ground. Four months into the construction process, the building is now going up quickly. Through this post, we'd like to provide an update on the project and also to share a few lessons learned.
Back in the 1950s, Ian's grandpa built his family's home. The care that he put into building that structure has been a source of family pride for more than 60 years. The pace of American life has changed since those days. With today's demands, it is increasingly rare for someone who works outside of the construction industry to have enough free time to invest in developing the necessary skills and then to build their own home from the ground up. A few people still pull it off, but most hire a building contractor. Rightly or wrongly, building contractors have a bit of a reputation. The best thing that has happened in our home-building experience was being able to hire our friend Jim as the contractor and main builder on this project. Jim is a dream contractor - experienced in all aspects of the construction process, who possesses a high level of integrity and holds the perspective that durable quality is more important than speed and ease of construction.
From time to time, Ian has been able to take some days of annual leave to go help the construction crew, and in turn, learn parts of the process. Yesterday the two of us (Ian and Amy) got to work on the building together as a couple, while the crew was off. We did some framing work and put up the grey lathing that you see in the image. This lathing will provide extra room for insulation in the walls and also a solid anchor for the building's metal skin. Our hammer has driven nails into every exterior stud in the house. Even if not to the same extent as Ian's grandpa, we've gotten to experience some of the fulfillment of getting to actively work in raising our own home.
As with any complex undertaking, there have been some unplanned incidents that make for amusing stories. Like on the day of slab-pouring, when a concrete truck drove off the end of our prepared driveway and got stuck in the sand. One truckload of fresh concrete had already been poured into the slab forms and was beginning to set. To have waited an hour for the special equipment needed to extricate the 80,000 pound truck from its ruts would have been a total disaster for our foundation and cost us big bucks. As a last-ditch effort, the empty concrete truck was brought back and chained behind the truck that was stuck. Two pickup trucks were then chained to the front of the empty concrete truck. The only thing that could have made this scene more memorable would have been for our tiny Hyundai Accent to be chained to the front of the convoy of trucks to lead the charge! Miraculously, they got the truck out and finished the pouring job before it was too late.
Some of the experiences have lead to important lessons learned. For example, we learned that it's a bad idea to assume - just because a subcontractor may be a professional who does the same job every day - that you don't have to check up on them. The subcontractors who laid out the forms for pouring the foundation were off in their measurements by a full foot. Rebar was laid out. 90,000 lbs of concrete was poured over it. After the slab was smoothed and had set for a bit, Jim's crew built a sand berm around it. The berm created a barrier that held a thin pool of water over the concrete slab when a water hose was run on it (Concrete that has dried very slowly is the strongest). Ian drove out to the farm nearly every day for a month to refill this inch-deep pond. It was only after all of this that we discovered the south side of the foundation slab was 30ft long, while the north side was 31ft long. $%&I*$7G%!!!!!!!! Of course, the subcontractor who made the error became unreachable. With some effort to find the humor in the situation, some hours spent cutting with a concrete saw, some more hours of Ian working the jackhammer, and a slight redesign to the driveway, we were back in business.
One final opportunity we had for learning that we would like to share came about through a recent conversation with a friend. In hearing that our new home will be "only" 1000 share feet of living space, the expression on her face kind of dropped. When we first sketched out the rough footprint of the home and rooms, we did it based on our own household's need for space without comparing it much to other homes. The conversation got us wondering, "What is the average size of the American home?". It turns out that it's 2,600 square feet. In fact, the last time that the average size of a new home was the same as ours was - you guessed it - back in 1950. The smaller size has allowed Jim to put quality materials into the building that will make it, in some ways, even stronger and more durable than Ian's grandpa's house while still staying within our limited budget. This has also been a blessing in helping us deal with some of the unexpected cost contingencies that can arise in home construction.
Next week, Jim's crew and some of our family will collaborate to erect the framework for the second story. We'll post updates from time to time. In the meantime, thank you Jim, and we hope that some of our readers will come by for a visit to the farm and house when construction is complete.
Comments